What is garment costing?
- Garment costing can be defined as a process of estimating and determining the cost of production of the garments. This includes all the costs involved. Such as- fabric cost, accessories cost, printing cost, embroidery cost, cost of making, and also the profit percentage of the factory.
- The cost of the garment is measured separately by the buyer and the manufacturing factory, then in the negotiation meeting, the final cost of the garment is determined.
- Proper costing of a garment is really important for both the buyer and the seller. If the proper cost of the product is being set, then it will be beneficial for both the parties and long term business relationship can be maintained between them.
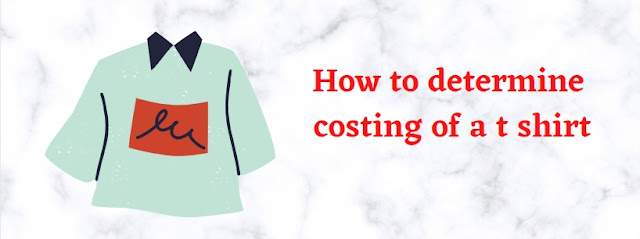
Different components of garment costing:
There are basically 10 components in garment costing. They are-
1. Cost of making (CM)
2. Fabric cost
3. Knitting cost
4. Dyeing cost
5. Finishing cost
6. Accessories cost
- Sewing thread
- Label
- Poly
- Button
- Carton
- Hanger
- Gum tape
- Embellishment (Print/embroidery)
7. Startup cost
8. Testing coat
9. Sampling cost
10. Commercial cost
![]() |
Costing components |
Different formulas:
Let us consider an example of t-shirt costing to get an idea about all the formulas:
Information:
- Factory expenditure/month = $500000
- Working days in a month = 26
- No. of machines = 500
- Total no. of garments to be made = 6500 pcs
- = 542 dozen
Some information about the garment:
- Yarn composition: 100% cotton slub yarn
- Construction: Body: Single jersey
- The base color of the fabric is white.
- No extra finishing work needed to be done.
- Printing is done on the front part of the garment
Now,
Formula of cost of making (CM) determination:
CM= (per m/c earning*no. of machines required for the style)/ (No. of production/hour*shift)
Again,
Per machine earning= Factory expenditure/ (working day in month*total machine)
So,
Per machine earning = 500000/ (26*500)
= $ 38.46
Cost of making = (38.46*17)/ (160*10) [T shirt production requires 17 m/c and hourly production is 160]
= $ .40/pcs.
= 4.9/dozen
= $4.9*542
= $2655.8
Also read:
Fabric consumption calculation of a basic T-shirt. | How to calculate fabric consumption of a basic T-shirt.
Sewing thread consumption formula and calculation of a basic t-shirt
Fabric cost:
Let’s assume that we need,
- 1.1 kg/dozen fabric for body
- 0.56 kg/dozen for neck rib
Yarn needed for body = (quantity required in kg/dozen* no. of dozen)
= (1.1*542)
= 596 kg
Again,
Yarn needed for neck = (quantity required in kg/dozen* no. of dozen)
= (0.56*542)
= 303 kg
Total yarn needed = (596+303+15% allowance)
= 1033.85 kg
So,
Fabric cost = (Total kg*price/kg) [28s slub yarn price = $3.4/kg]
= (1033.85*3.4)
= $3515
Knitting cost:
[Single jersey knitting cost = $0.20/kg
1*1 rib knitting cost = $0.25/kg]
Now,
Body fabric to be knitted = (Body yarn quantity*15% allowance)
= (596+15%) kg
= 685.4 kg
Body fabric knitting cost = (685.4*$0.20)
= $137.08
Neck fabric to be knitted = (Neck yarn quantity*15% allowance)
= (303+15%) kg
= 348.45 kg
Neck fabric knitting cost = (348.45*$0.25)
= $87.1125
Total knitting cost = $224.2
Dyeing cost:
[White color dyeing cost = $.80/kg]
So, Dyeing cost = (Total quantity of fabric*dyeing cost/kg)
= (1033.85*.80)
= $827.08
Finishing cost:
No finishing work is being done.
Accessories cost:
Sewing thread cost:
[On average 150 m thread/body is needed
One thread cone contains 4000 m thread that costs $.60]
Total quantity of sewing thread needed = (Total number of garments*thread required/pcs. of garment)
= (6500*150)
= 975000 m
= (975000/4000) cone
= (743.7+5% allowance) cone
= 255.8 cone
Sewing thread cost = $(255.8*.60)
= $ 153.48
Label cost:
[Main label price = $.20/dzn
Care label price = $.20/dzn
Price tag price = $.15/dzn]
Formula = (Total garments in dozen*price of label/dozen)
Now,
Main label = (542*.20)
= $108.4
Care label = (542*.20)
= $108.4
Price tag = (542*.15)
= $81.3
Total = (298.1+5% allowance)
= $313
Poly cost:
[Poly price = $.20/dozen]
Now,
Poly cost = {(542*.20) + 5%} allowance
= $113.82
Button cost:
No button is being used.
Carton cost:
[120 pcs of garment can be packed in a carton
Carton price = $1.3/pcs]
Total carton required = {(6500/120) + 5%} allowance
= 56.7 carton
So,
Carton cost = $(56.7*1.3)
= $73.71
Hanger cost:
[Hanger price = $1.45/dozen]
So,
Hanger cost = {(542*1.45) + 5%}
= $825.2
Gum tape cost:
[Gum tape price = $.60/dozen]
56.7 pcs. carton = 4.7 dozen carton
So,
Gum tape cost = $(4.7*.60)+5% allowance
= $2.96
Embellishment cost:
[Print cost = $3/dozen]
So,
Print cost = $(542*3)
= $1626
Startup cost = $1000
Testing cost = $20
So,
Sub-total cost = $11350.25
Sampling cost = $(11350.25*.015)
= $170.25
Commercial cost = $(11350.25*.035)
= $ 397.26
So,
Total cost= $11917.76
Cost/pcs = $(11917.76/6500)
= $ 1.83
Conclusion:
The process of costing and the individual prices of different elements may vary from time to time. But the overall process of determination of costing will remain the same.
0 Comments